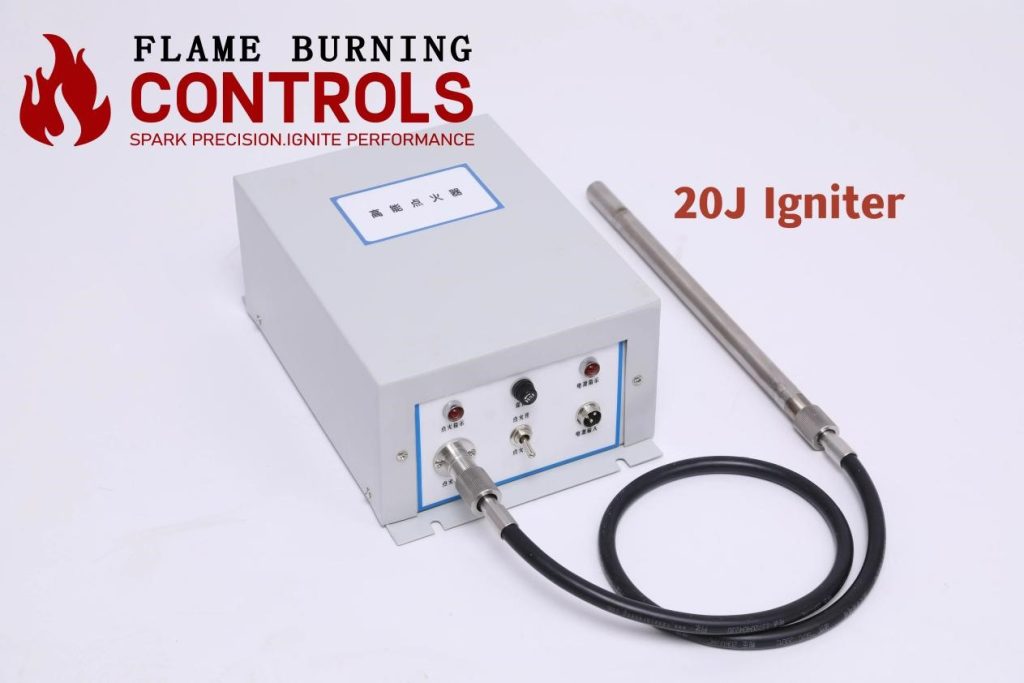
In the world of turbines, whether in aviation, industrial power generation, or marine applications, the role of a high-energy igniter is nothing short of crucial. These small yet mighty devices are the unsung heroes that kick-start the combustion process, ensuring turbines operate efficiently and reliably.
How High-Energy Igniters Work
High-energy igniters operate on a principle that involves storing electrical energy and then releasing it in a powerful, concentrated burst. They typically use a capacitor to store electrical charge. When the ignition process is initiated, the stored energy in the capacitor is rapidly discharged across an igniter plug. This discharge creates an intense spark, often with an energy output of around 12 joules in many gas turbine applications. This spark is hot and energetic enough to ignite the fuel-air mixture within the turbine’s combustion chamber.
For example, in a gas turbine engine, the high-energy igniter unit is usually mounted on the side of the engine. It has two high-energy igniter units, each feeding a separate igniter plug. This setup provides redundancy and ensures that there is always a reliable ignition source available.
Importance in Turbine Operations
Reliable Start – Ups: Turbines need a reliable ignition system to start up smoothly. In aviation, for instance, a failed ignition during takeoff or landing could have catastrophic consequences. High-energy igniters offer a high success rate in igniting the fuel mixture, ensuring that aircraft engines can start quickly and safely, even in adverse weather conditions.
Combustion Stability: Once the turbine is running, the high-energy igniter can also play a role in maintaining combustion stability. In some situations, such as when the turbine is operating at low power or in challenging environmental conditions, the ignition system may need to be activated to prevent a “flame out.” This helps in continuous power generation in industrial turbines and stable operation of aircraft engines during flight.
Fuel Flexibility: High-energy igniters enable turbines to use a variety of fuels. They can generate a spark strong enough to ignite different types of fuels, from light hydrocarbons to heavier fuels. This is especially important in industrial settings where the availability and cost of fuels can vary, allowing turbines to adapt to different fuel sources.
Types of Igniter Plugs Used
There are two main types of igniter plugs used in conjunction with high-energy igniters in turbines.
Older Version: Similar to a piston engine spark plug, but with a larger spark gap. This design allows for a more powerful spark to be generated, which is necessary for igniting the fuel-air mixture in a turbine’s high-pressure and high-temperature combustion environment.
Surface Discharge Igniter Plug: A more modern alternative. The end of the insulator of this type of plug is made from a semi – conductor material. When the high – energy discharge occurs, the semi – conductor material allows an electrical leakage. This ionizes the surface of the semi – conductor material, providing a relatively low – resistance path for the energy stored in the capacitor. The discharge results in a high – intensity flash – over from the hot electrode to the body of the igniter, which only requires around 2,000 volts. This type of plug has shown advantages in terms of durability and performance in turbine applications.
Advancements in High – Energy Igniter Technology
Over the years, there have been continuous advancements in high – energy igniter technology. One such development is the high – energy plasma igniter. This type of igniter aims to improve ignition efficiency. It consists of an ignition exciter unit and a matched plasma generator. The ignition exciter unit includes components like a control relay, a transformation isolating circuit, an oscillating impulse circuit, an arc maintenance follow current module, and a high – voltage transformer. The plasma generator has a fitting seat, a centre shaft, an insulator, a cathode, and an anode. This design not only improves ignition efficiency but also helps in cooling the electrode, thereby prolonging its service life. Additionally, with better cooling, the plasma ignition energy can be increased, enabling the ignition of low – grade fuels like heavy oil under more challenging conditions.
In conclusion, high – energy igniters are integral to the proper functioning of turbines. Their ability to provide a reliable and powerful ignition source is essential for the safe, efficient, and stable operation of these complex machines across various industries. As technology continues to advance, we can expect even more efficient and reliable high – energy igniter solutions to emerge, further enhancing the performance of turbines worldwide.